Charging and discharging batteries is a chemical reaction, but it's claimed that Li-ion is an exception.
Li-ion batteries are influenced by numerous features such as over-voltage, Undervoltage, overcharge and discharge current, thermal runaway, and cell voltage imbalance. One of the most significant factors is cell imbalance which varies each cell voltage in the battery pack over time and hence decreases battery capacity rapidly.
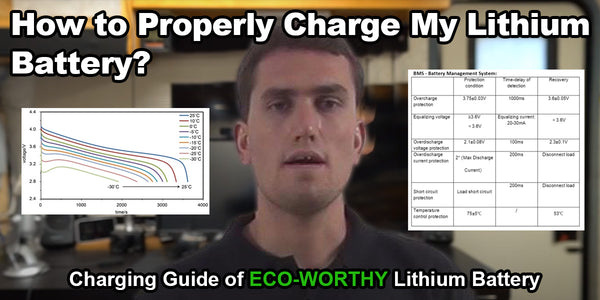
How to charge ECO-WORTHY lithium battery
You can charge your lithium iron phosphate batteries whenever you want just like your cellphone. Unlike lead-acid batteries, lithium iron phosphate batteries do not get damaged if they are left in a partial state of charge, so you don’t have to stress about getting them charged immediately after use. They also don’t have a memory effect, so you don’t have to drain them completely before charging.
There are two methods for battery charging:
1. battery charger(mains power)
2. solar panel (DC power)
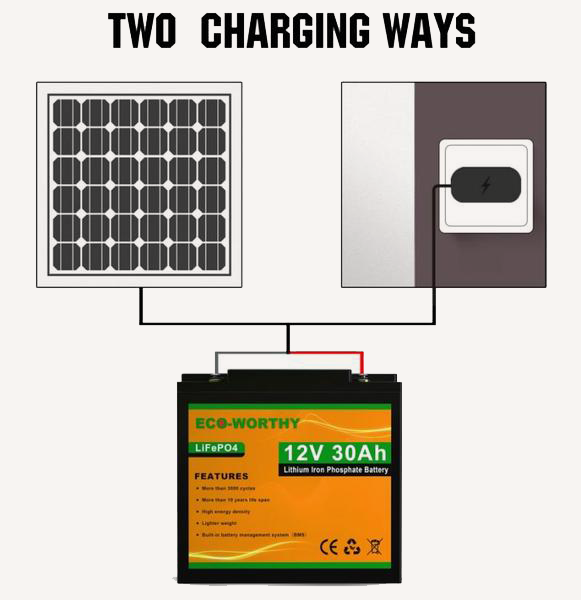
The most ideal way to charge a LiFePO4 battery is with a lithium iron phosphate battery charger, as it will be programmed with the appropriate voltage limits. Most lead-acid battery chargers will do the job just fine.
AGM and GEL charge profiles typically fall within the voltage limits of a lithium iron phosphate battery. Wet lead-acid battery chargers tend to have a higher voltage limit, which may cause the Battery Management System (BMS) to go into protection mode. This won’t harm the battery; however, it may cause fault codes on the charger display.
Li-ion Battery cell level and pack level control variables are needed to be maintained accurately for safe operation. These control variables are monitored and protected by the battery management system (BMS).
BMS is an electronic device that acts as a brain of a battery pack, monitors the output, and protects the battery from critical damages. This incorporates monitoring of temperature, voltage, and current, failure forecast or prevention, and data collection through communication protocol for battery parameter analysis. Battery state of charge (SOC) is the percentage of energy currently stored in the battery to the battery nominal capacity. One of the important key functions of BMS is cell balancing.
Of course, you can also use a solar panel to charge your ECO-WORTHY LiFePO4 battery, but please make sure to choose a proper controller, both PWM controller and MPPT controller are okay.
And as an SLA targeted 12V panel makes about 18V at full-sun full-load, such a 12V panel will provide more than enough voltage under all practical light conditions.
If you don't have a controller, you can connect the battery to the solar panel, too. The BMS inside will protect the battery most times.
But if there is a defect in the battery BMS, the battery will be damaged.
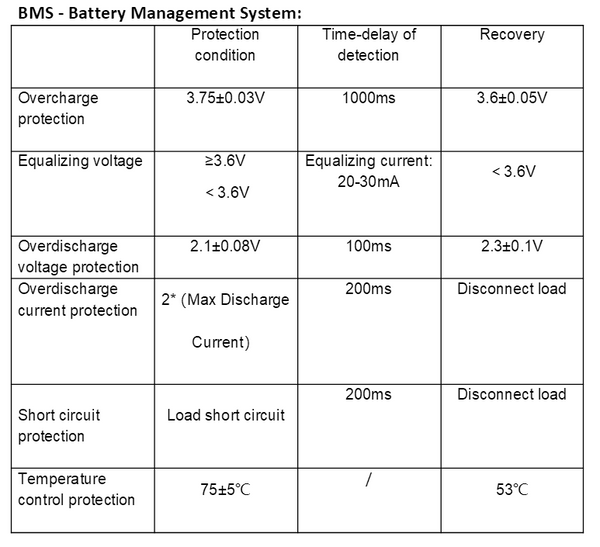
The ECO-WORTHY Battery Management System (BMS) performs three primary functions:
1. It protects the battery pack from being over-charged (cell voltages going too high) or over-discharged (cell voltages going too low) thereby extending the life of the battery pack. It does this by constantly monitoring every cell in the battery pack and calculating exactly how much current can safely go in (source, charge) and come out (load, discharge) of the battery pack without damaging it. These calculated current limits are then sent to the source (typically a battery charger) and load (motor controller, power inverter, etc), which are responsible for respecting these limits.
2. It calculates the State of Charge (the amount of energy remaining in the battery) by tracking how much energy goes in and out of the battery pack and by monitoring cell voltages. This value can be thought of as a fuel gauge indicating how much battery power is left in the pack.
3. It monitors the health and safety of the battery pack by constantly checking for shorts, loose connections, breakdowns in wire insulation, and weak or defective battery cells that need to be replaced.
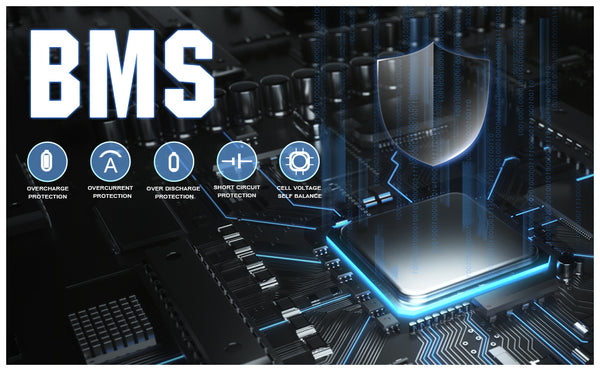
Unless you like living on the edge, DO NOT BUY a battery without BMS!
How to choose an ECO-WORTHY lithium battery charger? Can I charge my lithium battery with a lead-acid charger?
Lithium batteries are not like lead-acid and not all battery chargers are the same. A 12V lithium battery fully charged to 100% will hold voltage around 13.3V-13.4V. Its lead-acid cousin will be approx 12.6V-12.7V.
A lithium battery at 20% capacity will hold voltage around 13V, its lead-acid cousin will be approx 11.8V at the same capacity.
So if you use the lead-acid charger to charge your lithium battery, it may not be fully charged.
You can use an AC to DC lead-acid charger powered by mains power, as charge efficiency and duration are less of a concern, it must not have automatic desulfation or equalization modes. If it does, do not use it as there is a high chance of damage to the cells or battery. This can have a significant reduction in battery longevity. If it has a simple bulk/ absorption/ float charge profile, then it can be used to recharge the battery but must be disconnected once charged and not left in trickle charge/maintenance mode. It must also have a maximum output voltage of 13V-14.5V. When it comes to DC-DC chargers and solar controllers, you must change these to LiFePO4 specific models.
Our ECO-WORTHY battery charging parameters consist of the following:
✹Bulk/absorb: 14.2V- 14.6V. ✹Float: 14.6V ✹Equalization: 13.6V- 14.0V
But it would be best for you to choose a specific lithium battery charger. We have designed our own battery charger, perfect for lithium, LiFePO4 battery charging.
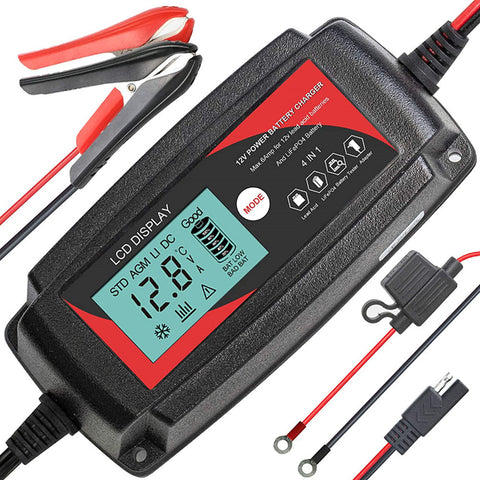
This device connects directly to the battery and is meant for single-battery charging. It’s great for those with trolling motor applications or those with battery systems connected in series.
How to use the charger properly?
Most LiFePO4 chargers have different charging modes, set them like this:
battery type: LiFePO4
battery cells: 4S
C (current): 10A (e.g. 0.3C for 30ah Battery)
Set the charger’s output current to no greater than the ‘0.7C’ rating of the battery. A recommended charging current no greater than 0.5C will help to maximize the lifespan of the LifePO4 battery.
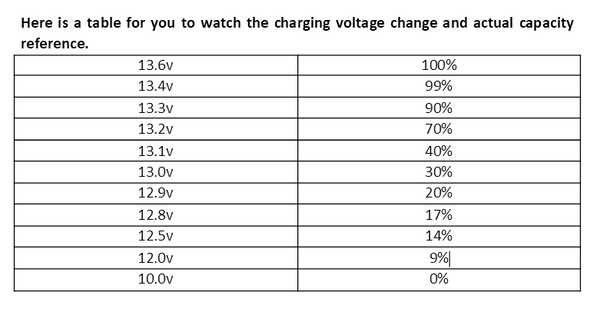
Battery bank charging/ Separate charging
ECO-WORTHY battery has a voltage limitation on battery BMS module, which allows a maximum of 4 batteries in series connection. And no limitation for parallel.
If you charge connected batteries together, it may cause that one battery to be fully charged and the other one not, because the BMS will cut off the current when detecting one high voltage when a single one is full.
E.g. 2*30AH batteries are not full when they get to one customer, the capacity and practical voltage varied when they got disposed of in the warehouse, one is 13.2V (70%), the other is 12.9V (20%).
The customer got them wired in series, and used a suitable charger to charge them together, after a while, the display revealed full capacity status when it detected one of the batteries got the 13.6V voltage, so the charging process was accomplished, and the charger cut off the current to the pack to avoid over-charging.
But actually, the other 12.9V battery was not fully charged after the current got off, so when the customer use the battery bank, he found that the capacity did not reach his expectation, because the total output power gets limited by the low voltage one.
So we recommend you get one charging balancer. Or just charge them separately.
If you found that the battery bank's total capacity could not reach what it should be after charging the pack to full voltage, you could disconnect the batteries, and test the voltage of each, to verify if some of them did not get fully charged in the process.
Can I charge lithium batteries in the cold?
Lithium batteries rely on chemical reactions to work, and the cold can slow and even stop those reactions from occurring. Unfortunately, charging them in low temperatures is not as effective as doing so under normal weather conditions because the ions that provide the charge do not move properly in cold weather. There's one hard and fast rule: to prevent irreversible damage to the battery, don't charge them when the temperature falls below freezing (0°C or 32°F) without reducing the charge current. Because the lithium batteries suffer from a phenomenon of lithium metal plating on the anode if charged at high rates in cold temperatures. This could cause an internal short of the battery and a failure.
Please look at the following table to see the relationship between the voltage and temperature.
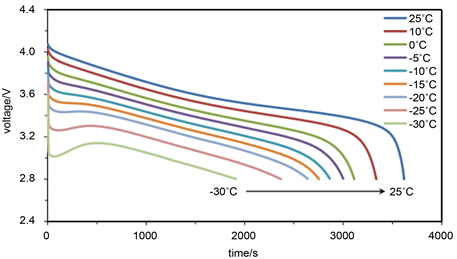
Can I leave the ECO-WORTHY lithium battery on charging all the time?
For a lithium battery with a low maintenance charging procedure and battery management system, it's perfectly fine and better than leaving them discharged for a long period. Regardless of whether it is a dedicated charger or a general charger, under normal conditions, it has a charging cut-off voltage, which means that it will stop charging at a certain volt. The same is true for the solar panel controller, and the controller can also be configured like this. The solar panel is directly connected for charging. If there is a problem with the BMS, it may be overcharged.
Can I recharge my lithium battery from my vehicle alternator?
Yes, but not necessarily to full charge, because most Alternators are adjusted for the lower voltage requirements of the vehicle Lead/Acid Battery (approximately 13.9V). Lithium Batteries require 14.4 to 14.6 Volts to fully charge. That being said, you can get up to approximately a 70% charge, depending on the depth of discharge and distance driven while recharging from your vehicle alternator.
It’s best to use a DC to DC charger, which helps protect and extend the life of your RV battery and not overload your vehicle alternator. Most DC to DC charger models have the same three-stage charging modes, and they will safely charge the battery and prevent alternator damage.
...